The meaning of 'rugged': 8 tests behind MIL-STD ratings
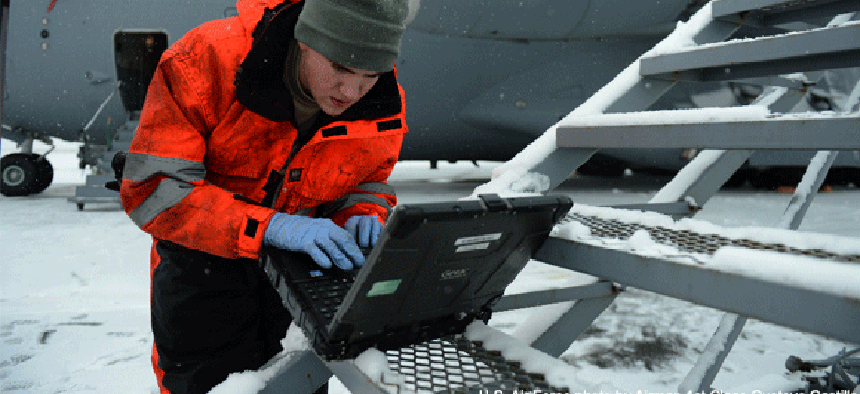
The U.S. Military Standard (MIL-STD) 810 tests are designed to let users know how equipment will perform in harsh environments. Here are the eight tests most commonly applied to computing devices.
When an agency considers a device that is said to be “rugged” or “ruggedized,” what does that mean, exactly? Sure, it means it can take more punishment than an everyday laptop or phone, but in which ways? An object that withstands the cold might not also be good at taking impact, for example.
The U.S. Military Standard (MIL-STD) 810 gives agencies a guide. It was introduced in 1962 to provide a series of tests to simulate how materiel would hold up to environmental stress during its operational lifetime. It has been revised several times over the years, the most recent being Revision G in 2008. It details 28 different testing methods that cover everything from temperature to fungal infestation to gunfire. Of course, not all of them apply to every specific item — what applies to a gas mask or Kevlar vest doesn’t necessarily apply to a tablet.
Agencies buying a rugged device that’s MIL-STD rated, should know what those ratings mean. Here are eight tests used to determine a computing device is rugged.
Method 501.5 – High Temperature
This testing method is broken down into three procedures.
- Procedure I (storage) exposes the device to high temperatures while it is turned off, and its purpose is to test the durability of the physical materials that make up the device.
- Procedure II (operation) is concerned with how the device puts up with heat while having it turned on and used. Procedure II is actually in two parts:
- Constant exposure tests are usually reserved for devices that are meant to be in continuous proximity to an artificial heat source.
- Cyclic exposure tests are more indicative of real-world conditions. The range of temperatures used in an operational cyclical test go from 30 degrees Celsius (86 degrees Fahrenheit) to upwards of 49 degrees C (120 degrees F). The temperature needs to cycle from one end to the other a minimum of three times while testing that the device functions at every point in the test.
- Procedure III (tactical-standby to operational) gauges how it works under operational temperatures after having been exposed to higher storage temperatures.
Method 502.5 – Low Temperature
This test also has three procedures to determine how the device will behave in low temperatures.
- Procedure I (storage) is much the same as the high temperature test.
- Procedure II (operation) testing involves slowly cooling the device to the low temperature in the appropriate range and leaving it at that temperature for at least two hours, checking visually to see that it is still functioning during that time.
- Procedure III (manipulation) investigates the ease with which the device can be set up and disassembled while wearing heavy winter clothing.
Method 506.5 – Rain
This is one of the tests for any device advertised as water resistant, and its results help determine what Ingress Protection (IP) rating the device should get for liquid protection. There are three procedures.
- Procedure I (rain and blowing rain) is for devices that will be used outdoors. The water is at least 10 degrees C colder than the device, and wind sends the water droplets at the device for 30 minutes.
- Procedure II (exaggerated) is for large materiel that can’t fit inside a rain chamber, such as sheds, so isn’t used for computing devices generally.
- Procedure III (drip) is for devices that would be protected from rain, but may still be exposed to some falling water. The water temperature is 10 degrees C lower than the device, and it drips along the device’s upper surface from a distance of at least one meter for fifteen minutes.
Method 507.5 – Humidity
This method determines how well the device can hold up to warm, humid air.
- Procedure I (induced (storage and transit) and natural and cycles) involves three 24-hour cycles representing conditions that may occur during storage and transit, and three more that simulate natural environment cycles.
- Procedure II (aggravated) exposes the device to more extreme temperature and humidity levels than those found in nature, but for shorter durations. Some testers choose Procedure II for some materiel because it produces results quite a bit more quickly, even though they may not completely reflect what will actually be encountered.
Method 510.5 – Sand and Dust
How good is the device at keeping out particles?
- Procedure I (blowing dust) tests ingress of dust particles that are smaller than 150 micrometers (μm). To test Procedure I, start with the wind at 8.9 meters/sec (1750 feet/min). Then feed the dust at an average concentration of 10.6 grains per cubic meter (0.3 grains per cubic foot). Maintain for at least six hours at standard ambient temperature, rotating the device to eventually expose all sides. Then raise to operating temperature, lower the wind speed, stop the dust, and test for another 6 hours, rotating the device as necessary.
- Procedure II (blowing sand) tests ingress with particles that are between 150 μm and 850 μm. The test starts at operational temperature and requires much higher winds – 18 to 29 meters/sec (40-65 mph) in order to move the heavier particles. The sand concentration will vary widely depending on the target environment — the high end simulates being near aircraft, for example. The test is run for 90 minutes for each face the device has, stopping the sand and wind so it can be rotated safely.
Method 512.5 – Immersion
This method determines if a device can withstand being submerged or partially submerged in water, or just splashed a lot, and be able to function after or even during the process. This test will determine if a device warrants an IP rating with a second number as high as a 7. There is one procedure applicable to electronic devices:
Procedure I (immersion) covers putting any part of the device underwater. The test starts by weighing the device. Then every panel, door or cover that might be opened during use is opened and closed three times each. To test the affects of a temperature differential on the seals, the device can be warmed up to 10 to 27 degrees C above that of the water. Then the device is placed into the water so that its top side is one meter below the surface for 30 minutes. Partial immersion is used in cases where the device is designed to float, but other than the depth, the test is largely the same.
Note that the specification does not cover the highest IP rating for liquids – 8, which involves depths of more than one meter and longer durations, and would have to be verified independently of this MIL-STD.
Method 514.6 – Vibration
This method is one of the most complicated tests in the entire MIL-STD – all told, it takes up 83 pages of the 804-page document. Generally it is designed to determine if a device can withstand the vibrations it would be exposed to during its lifecycle. What types of procedures a device is exposed to will be determined by what life-phase it is in (manufacture, transportation, operational or supplemental) and where it is located (in a facility, a certain type of vehicle, etc.). This calculation puts it into a numbered category that determines specifically which testing procedure will be necessary.
Most of the tests involve using laboratory shakers set to different levels to simulate being on a vehicle or carried by a person. Variations in the vibrations’ wave form, frequency and intensity will change depending on the type of device and the environment being simulated, as will the actual duration of the testing.
Method 516.6 – Shock
This is probably the method that is cited the most by manufacturers and agencies alike. Part of this test method is sometimes referred to as the “drop” test, and it gauges how well a device holds up to impacts while falling from certain heights. The tests are designed to determine how well a device can put up with general physical abuse while in operation, but not from factors such as nearby explosions (these are covered in separate methods).
There are eight different procedures to choose from that each use different ways to cause shock or impact, but Procedure IV (transit drop) is the most often cited. The test was primarily designed for materiel that is loaded or unloaded from a vehicle, or taken off of a shelf, but for mobile devices it could certainly apply to nearly any operational instance.
How extensive Procedure IV gets is determined by the object’s weight. Personal computing devices would fall into the first category, which is for weights of less than 100 pounds and lengths of less than 91 cm (36 inches). The floor of the drop zone is two inches of plywood over concrete, which was determined to be the most common surface a device was likely to land on. Testers drop the device from a height of 4 feet on each of its six faces, 12 edges and eight corners, for a total of 26 drops. They visually inspect for damage and determine whether it still works after each drop. If a manufacturer requests, the 26 drops can be divided among five identical items.
Note that many manufacturers, particularly those of larger notebook computers, cite that their products were tested up to a shorter distance. If an object’s longest dimension exceeded 91 cm, then it would be dropped from 76 cm (30 in), but no portable computer is that large. Conversely, many makers of smaller items cite a drop distance in excess of the requisite 112 cm (4 ft.). Note also that the method only requires drops from the maximum height, although many testers choose to perform the 26 drops at each foot level up to and including the maximum.
NEXT STORY: Appian BPM gets more social and mobile