IoT conundrum: How to power buried sensors
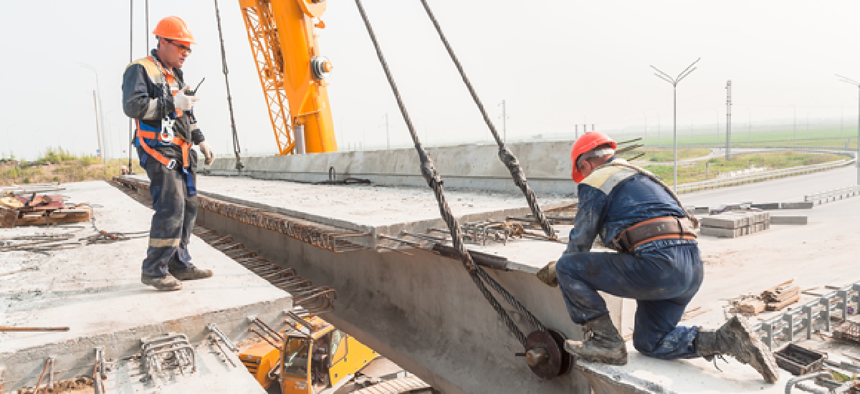
A researcher at Michigan State University has developed technology that can generate electrical power to buried or implanted sensors.
Even in its early stages of deployment, much of the Internet of Things will be hidden from users. Sensors will be buried in concrete, for instance, detecting signs of infrastructure decay or post-seismic damage. And tiny sensors will be implanted inside human bodies to detect problems with heart valves.
Of course, it's not practical or perhaps even possible to change the batteries of sensors buried inside a bridge or the foundation of a building, so those sensors will have to be self-powered.
That’s just what Shantanu Chakrabartty has developed – tiny, self-powered sensors capable of regenerating electrical energy. The trick is a tongue-twister technology called “piezoelectricity-driven hot electron injection.”
"Piezoelectricity is something that converts mechanical energy into electrical energy," explained Chakrabartty, an assistant professor of electrical engineering and computer engineering at Michigan State University. "What hot electron means is that the voltage that this electricity generates is large enough that it can create electrons that have a lot of energy."
Put simply, when something presses on one of Chakrabartty's sensors – developed under grants from the National Science Foundation – the mechanical force is translated into electrical energy. The charge that is generated is then sufficient to be saved in the sensor's tiny on-board flash memory. That means sensors implanted in roadways or bridges could be powered by the vibration of passing vehicles.
"Think of a box with holes that is filled with sand, and the sand corresponds to electrons," said Chakrabartty. "When one shakes the box, some of the sand will pop out of the holes. The sand that pops out represents the hot-electrons or high-energy electrons. By measuring the amount of sand that pops out, one could infer how hard one shook the box. And by changing the size of the holes one could detect different levels of mechanical excitation. This is equivalent to changing the electronic threshold on the sensor."
When a network of such sensors is deployed inside structures – whether buildings or, say, turbines in a wind farm – the readings can also give engineers critical and detailed data about the stresses experienced by the structures and their potential for failure.
According to Chakrabartty, the sensors developed for infrastructure sensing are approximately an inch in diameter. In-body sensors, on the other hand, are approximately a cubic centimeter in size.
For the present, he says, the devices don't generate enough energy to transmit data. "But as long as we can record the event and how many times that event occurred later on we can retrieve that information using an RFID scanner," Chakrabartty said. "For the medical sensors we use a diagnostic ultrasound to ping the sensors and retrieve the information."
Chakrabartty's sensors are already being deployed to the field – and a private-sector company named Piezonics has been formed to develop and market the technology, said Chakrabartty. In the meantime, he is still working on improvements.