How data management can cut cities’ hazardous waste costs
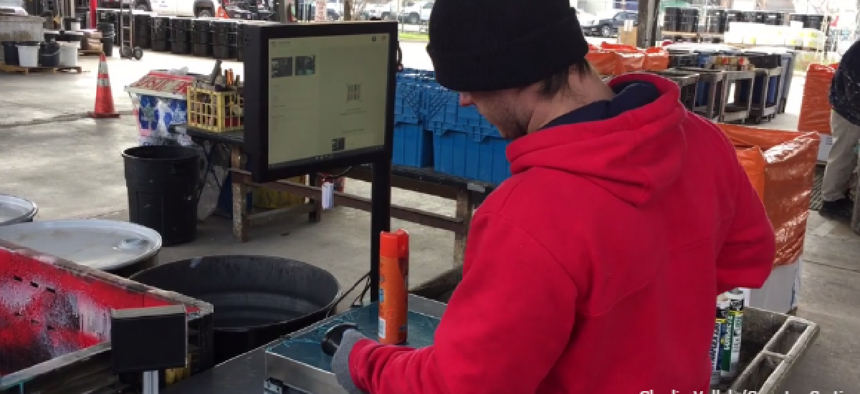
Connecting state and local government leaders
A startup’s sorting technology can help cities reduce the costs associated with disposing of household hazardous waste.
Most cities have collection sites where residents can bring household hazardous waste that should not be included in the regular waste stream -- paint, pesticides and batteries, for example. These items are usually hauled off from the collection site to an incinerator on the city’s dime.
Yet many of those products can still be used, said Chris Ripley, CEO and founder of Smarter Sorting, a company that helps cities sort their waste and send unused products to businesses that need them – a process that increases waste diversion and reduces costs.
The startup was the third-place winner in the Civic I/O Mayors Match Up, which was hosted by the U.S. Conference of Mayors and the City of Austin at the South by Southwest conference in April. The pitch competition targeted common problems cities face, and the solutions were judged on their uniqueness, scalability and potential for revenue.
Take bleach, for example, which frequently shows up at waste sites but which slaughterhouses can use for sanitizing. They don’t care if the bleach is from Clorox or Scrubbing Bubbles or if it smells like pomegranate, Ripley said, they are just interested in the product’s sodium hypochlorite.
Smarter Sorting provides household hazardous waste management sites with the technology infrastructure to sort these products, which are currently categorized by hand. “These items are optimized to be sorted by computer,” Ripley said. “They have barcodes.”
Employees scan an item’s bar code, place it on a scale where it is weighed and photographed. The software uses the bar code and image to sort through databases from retailers and manufacturers to provide a complete data record that includes the chemical composition and even the shipping regulations.
Once these items are identified, a touch screen tells the worker how to sort the item -- whether it should go to an incinerator or into any number of bins where it will be diverted to a business that needs it. That identification allows cities to turn bins of mixed chemical waste that would be incinerated into products that are easier to ship and place.
The technology must contend with that barcodes have been used by manufacturers more than once, Ripley said, which means scanning an old can of paint could return results for a newer, unrelated product, but Smarter Sorting uses machine learning to avoid this. “Computers are very bad at breaking this tie, so we had to create technology that can decide between [different options],” he said.
The company makes money by hauling off the sorted waste at 10-15 percent less than cities currently pay haulers to take it to the incinerator, then charging the buyers of the recycled chemicals 75 percent less than they’d currently pay.
The Portland, Ore., metro area is piloting the Smarter Sorting’s solution. Jim Quinn, the program manager for the area’s hazardous waste collection facility, said Portland’s aim might be a little different that from other cities because the state is proposing legislation that would hold the manufacturer partially responsible for helping dispose of a product it made.
“The manufacturers who make and profit from these products should have a hand in dealing with all of the leftovers that are out there,” Quinn said.
Much of the push-back from industry on this legislation, Quinn said, is related to how the responsibility is allocated among manufacturers. In a similar program in Canada, facilities take a representative sample of the waste and hand count the products originating from various manufacturers. That allocation is then applied to the whole collection.
“The system they have, no one is really happy with,” he said. “That’s where the work of Smarter Sorting comes into play.” Smarter Sorting would provide raw data on the exact number of products from every manufacturer.
The data created by Smarter Sorting also provides metrics to city managers and that can be used in cities' educational outreach regarding household hazardous waste. “Having a clearer picture of what products are already out there will help focus those efforts,” Ripley said.
Additionally, manufacturers also get valuable insight, he said. If a collection facility knows that 85 percent of fire ant poison is still 75 percent full when it arrives at a waste site, then the manufacturer would benefit by knowing it could sell the product in smaller quantities for not much of a price difference, he suggested.
The company has active pilots with Austin, Texas; Portland; Salt Lake City; and Mesa County, Colo., as well as with Habitat for Humanity. The nationwide launch of the technology is expected in August.