Giving robots a (better than) human touch
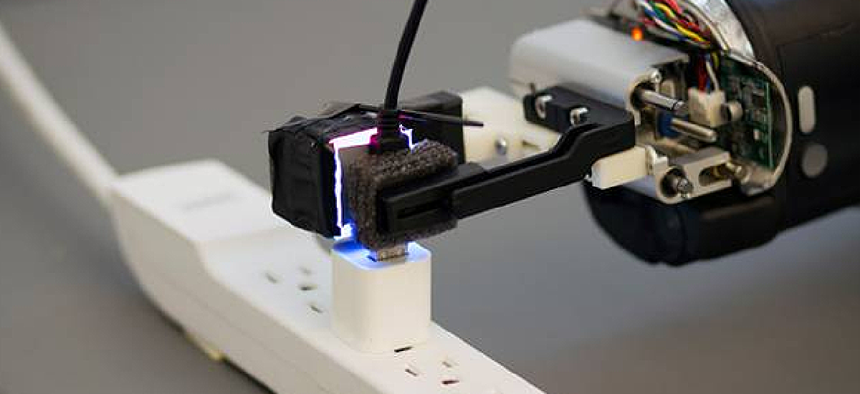
Researchers have just demonstrated a device with an optical sensor that can grab an unattached USB cable and insert it into a USB port.
It’s on old joke. “What’s the correct way to insert a USB cable?” Answer: “The opposite of the way you first try.” And even when you’ve discovered which way is correct, it usually takes some fumbling to get the cable into the port.
The point of the joke, of course, is that cable designers have not made it as easy as we might expect for humans to perform the seemingly simple task of inserting a cable.
And if it’s difficult for humans, how much more challenging would it be for robots? Yet if we are to further automate such places as data centers, hospitals and auto assembly lines, researchers will need to develop machines that are at least as good as humans at manipulating cables and other objects.
Researchers at MIT and Northeastern University have just made progress toward the goal by demonstrating a device that can grab an unattached USB cable and insert it into a USB port. Surprisingly, the tactile sensor of the device uses optics instead of pressure sensitivity to “feel” in guiding the cable to its destination.
The GelSight sensor has a layer of transparent synthetic rubber on one side that conforms to the object it is pressed against. Light bouncing off the magnetic paint that covers the layer is measured and analyzed to detect not just the shape but the amount of pressure being applied to the object.
“The GelSight sensor is interesting because it has high resolution in sensing,” said Robert Platt, an assistant professor of computer science at Northeastern and the research team's robotics expert. “It detects a lot of detail in the surface texture of the things that it is touching.”
In fact, the sensor is roughly 100 times more sensitive than a human finger.
The robot-mounted GelSight sensor is actually a lower-resolution version of the orginal GelSight sensor developed by team leader Edward Adelson, professor of vision science at MIT.
But while the new sensor offers less resolution, it’s also much smaller, small enough to fit on a robotic gripper. And the algorithms developed by Adelson’s team are fast enough to give the robot feedback in real time, which is what allows the robot to make the adjustments necessary for a successful insertion.
That capability, says Platt, has widespread potential applications. “We came up with one application for our testing, which is cable insertion,” said Platt. “To be honest, that’s a big one because cable insertions – while they seem like a small thing – are a big thing in manufacturing. People spent a lot of time inserting cables, and if you can automate that …”
NEXT STORY: DARPA in search of universal translator tech