From the workbench to the sky: 3-D printed drones
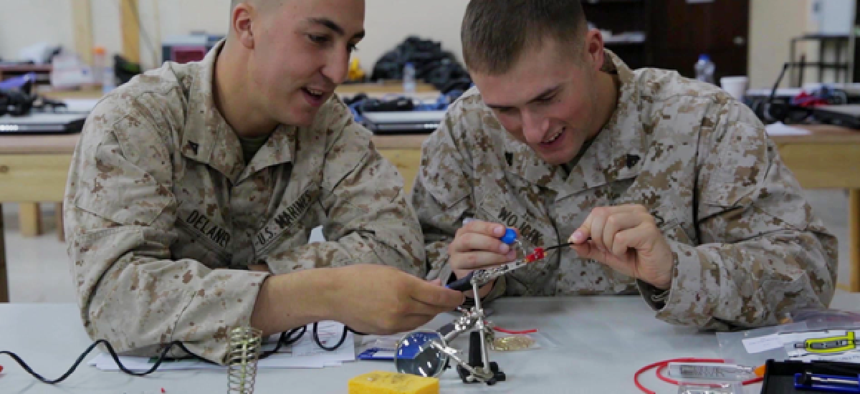
Nibbler, the Marines' 3-D printed drone, can be controlled by a smartphone, tablet or radio and customized for carrying ammunition, gathering intelligence and conducting surveillance.
The Marines are demonstrating their can-do attitude with the use of the "Nibbler," a 3-D printed drone that can help supply forces in the field and provide “over-the-hill” intelligence, surveillance and reconnaissance.
Nibbler is inexpensive, portable and easy to repair. It can be customized for carrying ammunition, gathering intelligence and conducting surveillance and can be controlled by a smartphone, tablet or radio controller.
Marines have been training on how to solder, wire, program and construct the system, which takes about six hours to build.
“Our team is very enthusiastic about the Nibbler, but even more enthusiastic about what it represents for the future,” said Capt. Chris J. Wood, who oversees innovation efforts at the Marine Corps’ installations and logistics branch.
3-D printing gained an early following in the military because it was seen as a solution to the perennial problem of shortages of spare parts for aging weapon systems. The Marines have embraced the technology, which they see as compatible with their “adapt and overcome” culture.
“Imagine being in a forward deployed environment, and just like Amazon, you can ‘order’ the weapons and equipment you need for the next day’s mission from an entire catalog of possible solutions,” Wood said. “These solutions can all be upgraded literally overnight, in order to integrate new components or adapt to new requirements. On a very small scale, Nibbler shows us that this is possible right now.”
Empowering Marines to manufacture equipment and parts as needed has enormous ramifications, Wood said. “It represents a revolution in the future supply chain.”
If a unit were to deploy with 12 different unmanned aerial systems, he said, “we would have to take 12 or more different types of packaging and associated sustainment parts.” The goal is to have a “small manufacturing capability” locally, he said. All that would be needed is a desktop printer, a box of components and a spool of plastic 3-D printing filament, Wood said. He envisions a “near-infinite set of different UAS that we could produce from those basic elements.”
From a cost perspective, 3-D printed drones should save the government money in the long run, Wood said. Because the military only buys in small numbers, the upfront cost of a military 3D printed drone is higher than those $300 drones that are sold commercially. “However, it is orders of magnitude less expensive than any military-use UAS with similar performance,” Wood said.
A drone made by Marines in a trailer obviously will not be a substitute for high-end aircraft made by Pentagon contractors, but that is beside the point. “Ultimately, it's about optimizing specific mission needs to the equipment we use to fight those missions,” Wood said. Many of the requirements today could be met with lower end equipment, and often the priority is to get things fast, which is one reason this technology is catching on. “Additive manufacturing and localized manufacturing allows us to do this at a scale and speed never before seen,” he said.
Deputy Commandant for Installations and Logistics Lt. Gen. Michael G. Dana has been a champion of 3-D printing. Speaking at Deloitte’s Additive Manufacturing Forum in May, he told industry executives that they should jump on the bandwagon.
Marines clearly have ambitious goals but recognize the technology and the business culture are not there yet. There are no expectations that, today, a Marine will buy a $2,000 printer and make military-compliant axles. But they do see a future of “micro-factories” propping up around the United States, in overseas combat zones and even on large Navy ships where troops will make spare parts and systems like drones, trucks and small radios. “On demand, as needed, closer to the point of need,” said Marine logistics expert Lt. Col. Howard Marrotto. “That’s something we don’t have. We assume when we forward deploy, we bring every single thing we might need, just in case. The assumption today is that the supply chain may or may not support our needs.”
Marrotto said at the Deloitte forum that the Marine Corps needs help from the private sector to better grasp the economic incentives and the potential capabilities of digital manufacturing. “We need to understand where the technology is going, the art of the possible,” he said. The good news for the military is that incoming recruits are likely to be more familiar with 3-D printing than their superiors. Kids are learning 3-D printing in schools, which means a “ready workforce.”
The Marine maker movement appears to be gaining momentum. Four labs are being built and 25 “maker units” have been deployed in the United States and overseas. “Maker labs will be open to everyone, regardless of occupation, rank, or prior experience with design and prototyping,” declares the Marine Corps on its website. Maker units are equipped with a 3-D printer or mini-mill along with a laptop and software to support design and production. A unit of any size or type may request support from Marine Corps Installation and Logistics to explore becoming a maker unit.
There is one lingering concern in military 3-D printing: Protecting sensitive data from hackers and malware. How the military would bring cybersecurity into digital manufacturing so far has stirred “a lot of discussion but not a lot of action,” Marrotto said. The issue is how to protect a system’s “digital thread,” the term used in the industry for data associated with each product throughout the manufacturing lifecycle.
The Pentagon has not yet addressed this issue. Industry experts suggest the military use blockchain to ensure the integrity of the data. Blockchain won't stop cyberattacks, but it gives users tools to audit data for unauthorized changes.
This article was first posted to Defense Systems, a sibling site to GCN.