County tests feasibility of 3D-printed affordable housing
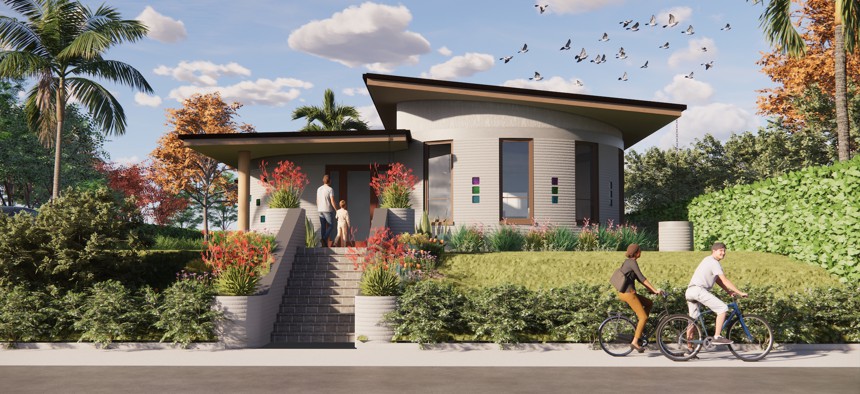
Rendering of a proposed 3D-printed home in Santa Barbara County, California. Courtesy of the Santa Barbara County Association of Governments
Santa Barbara County is using a state grant to 3D-print an affordable home in what it hopes will be a demonstration project other communities can learn from.
What happens when you combine a faith group, a state grant, a local housing trust fund and 3D-printing technology? For Santa Barbara County in California, the answer appears to be an experiment in affordable housing.
The Santa Barbara County Association of Governments recently announced that it will receive $5.3 million through California’s Regional Early Action Plan program, an initiative that funds projects that simultaneously address housing and climate change challenges. The funding will help support seven projects, including the construction of a prototype 3D-printed home that will allow the county to better understand how new technology could help address the affordable housing crisis.
Santa Barbara County is not the first to turn to 3D printing for housing solutions. Chattanooga, Tennessee, for instance, is using the technology to build temporary shelters for people experiencing homelessness. In Greeley, Colorado, the city and state are working with Habitat for Humanity and the robotics company Alquist to build 300 affordable homes and develop a 3D-printing workforce.
Santa Barbara County, meanwhile, is exploring the new technology as a means of quickly developing long-term affordable housing and leveraging relationships with community-based organizations to bring its own project to life.
“We liked the 3D printing because it seems very flexible,” said Jennifer McGovern, president and CEO of the Housing Trust Fund of Santa Barbara County, a co-sponsor for the project.
“It could do a variety of types of housing, everything from tiny homes to accessory dwelling units and potentially multifamily.”
The Housing Trust Fund is partnering with the Cambridge Drive Community Church on the project. They will construct the first 3D-printed home in the county, and likely one of just a handful that exist in the state, McGovern said. The home will be built on underutilized church property and will have a restrictive covenant, meaning it will need to remain affordable for at least 30 years in exchange for financing. The church already has ties to a local organization that serves women and children experiencing homelessness, and a family from that program will eventually live in the 3D-printed home.
The average cost of a home in Santa Barbara County is about $870,000, a nearly 10% increase over last year, according to the real estate company Redfin. The county is building the home in Goleta, a small city in the southern part of the county where a single-family home typically costs somewhere in the neighborhood of $1.5 million, McGovern said. The total cost of the 3D-printed project has yet to be determined as the organizations wait on concrete quotes, but McGovern said she hopes to see the new home completed at no more than half that price, paid for in part with $375,000 from the state grant.
“It's still expensive for our area,” McGovern noted “But it's going to be much less.”
Affordability won’t be the home’s only star quality. The “ink” of the 3D printer will be made of climate-resilient concrete, an increasingly desirable feature as wildfires blaze across Southern California, McGovern said.
3D-printed homes are built by robotic arms with nozzles that deposit layers of material to create walls. It’s a much faster process than traditional construction, in many cases taking no longer than a few days. That can save developers a huge chunk of change as it limits interest accrued on a construction loan, McGovern said.
But other parts of the construction process will still take time, she added. A foundation must still be laid and windows, doors, plumbing and electricity installed by contractors. Plus, a new technology like 3D printing doesn’t exactly make navigating red tape quick or easy.
Working with new building technology inevitably presents challenges that don’t exist for other methods of housing construction. One of the biggest is navigating building codes. 3D technology is so new that many cities and states don’t have ordinances or regulations to guide construction. That adds an extra step for developers, McGovern said.
Apis Core, the 3D printing company executing the project in Goleta, worked with a third-party engineering firm to study the structural integrity of its printed walls. The study found that the 3D-printed walls were comparable to traditional concrete masonry, which is allowable under current California building codes. With those results in hand, the project’s leaders secured approval for a single-story 3D-printed home from local building officials. That process, however, would need to be replicated for multi-story buildings, especially in an earthquake-prone state like California.
The Santa Barbara County project leaders plan to write up their experience as a case study for other communities that want to learn about 3D-printed homes, McGovern said. “We're also going to film the 3D printing and disseminate the whole study… and whatever the findings are just to get it out there as an option for people.”
“I think [3D printing homes] has a lot of appeal,” McGovern said “The speed and potential savings and the climate resilience and fire resistance … is important in many California communities.”