How tech helps stretch asset maintenance talent
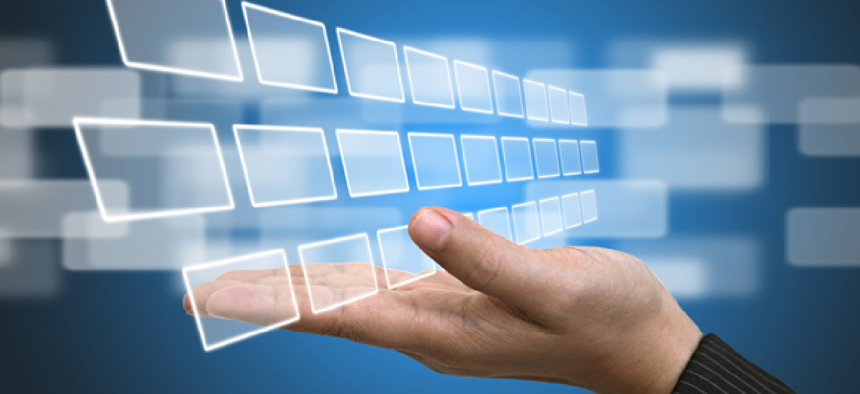
Connecting state and local government leaders
An advanced enterprise asset management solution with built-in analytics and artificial intelligence is a more effective way to help overcome the shortage of skilled technicians.
Of the many challenges the public sector faces, maintaining physical assets is one of the most pressing and complex. With budgets stretched thin and a shortage of maintenance technicians, the difficulties compound. However, technology can help alleviate the burden with tools to optimize the existing asset maintenance workforce and increase productivity.
What is the back-story?
Many industries cite a shortage of skilled workers as a major hurdle. With retiring baby boomers leaving gaps that incoming millennials and Generation Z workers are not filling, the public sector, notorious for modest pay structures, has been hit hard.
At the same time, government facilities and assets are increasingly complex, often with embedded sensors and connections to internet-of-things networks. It's easy for the maintenance crew to fall into the chaotic cycle of making one emergency repair after another, unable to get ahead of the demand and build a prescriptive maintenance strategy.
Technology can help overcome the pressures
Agencies need a strategy to stretch the abilities of their existing teams, allowing technicians to work smarter. An advanced enterprise asset management (EAM) solution with built-in analytics and artificial intelligence is a more effective way to help overcome the shortage of skilled technicians:
Knowledge base. Some advanced EAM solutions contain tools to help the call center triage requests for service. For example, a county’s call center may experience numerous calls about seemingly non-critical issues —but such issues can potentially escalate to major traffic or safety concerns. Using the knowledge base of scripted questions and risk assessments, call center workers can make informed decisions and accurately determine priorities prior to dispatch.
First-call resolution. Collecting the right information upfront about service requests will help pinpoint the location and identify the assets involved as well as any personal property issues. Such information can help technicians determine if specialized replacement parts or tools should be brought to the repair site.
Checklists. Advanced EAM solutions contain highly flexible checklist capabilities that can be used to capture the “tribal knowledge” of the existing team and document a wide variety of best practices developed over years of experience. This capability allows the experiences of senior technicians to be documented in formats easily consumable by the next generation.
Automated workflows. The shortage of skilled technicians means maintenance teams are often forced to hire candidates with little training or experience. Fortunately, advanced EAM solutions can automate maintenance processes, stepping users through prescribed workflows, automatically opening the next logical screen and pushing relevant contextual data for consideration. Such automation helps recent recruits follow procedures with minimal supervision, making it easier to onboard new technicians.
Augmented reality. Modern image recognition, sensor connectivity, AI and machine learning capabilities help users employ innovative tools, like digital glasses, to view added information about an object while in the field. Proximity to the asset or verbal cues can launch overlay screens that depict the component configurations, such as service history and warranty status.
Behind the scenes. Screens accessed by glasses or on mobile devices can also be used to see what is beneath the surface level, such as power lines that may be inside walls. Such critical data about an asset can be helpful in making quick decisions about best solutions.
Shared visuals. When apprentices or junior-level technicians are dispatched to worksites, a senior-level technician at the central office can offer feedback as needed to multiple technicians at once.
Drones for inspections. In some regions, municipal assets may be spread over a wide terrain, including dangerous places, like mountain ledges. Having a large enough staff to dispatch technicians far and wide can be unrealistic. Drones can be used for the “leg work” of technicians, sending back video that can help detect maintenance requirements.
Virtual reality. New technicians can get valuable practice time on virtual reality simulations, providing them with the opportunity to boost skills and confidence levels before being dispatched to work on mission-critical equipment.
Predictive analytics. Public-sector offices and agencies are often asked to forecast their budget for assets, equipment and workforce needs. With the shortage of skilled technicians, it becomes even more important that the maintenance team has insight into workforce needs. With predictive analytics in EAM solutions, users can project likely outcomes based on patterns.
The shortage of skilled maintenance technicians is not going to disappear overnight. However, with technology helping employees work smarter, existing technicians and new recruits can better manage the workload. These are important steps for building the workforce of the future -- and maintaining an agency's critical assets. Do not let being short-handed get in the way of protecting the assets on which constituents depend.
NEXT STORY: How IARPA invents its way to security