More efficient flight with flexible, morphing wings
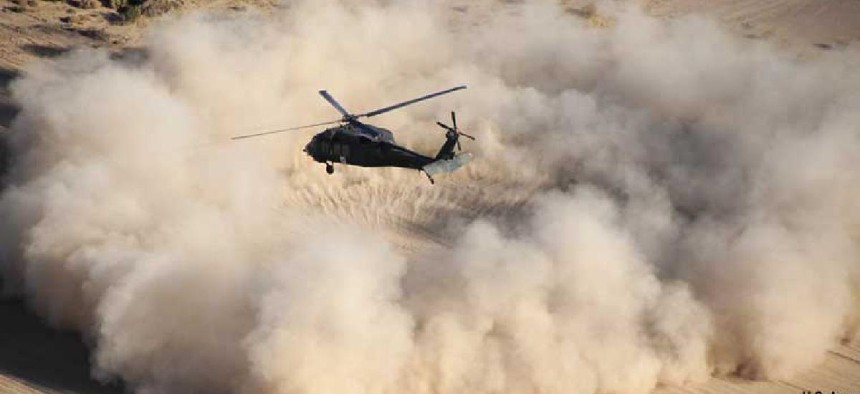
Army researchers have developed a tool that will quickly compute how the wings on vertical-lift aircraft can adjust their shape during flight to optimize performance.
Army researchers have developed a tool that will allow wings of vertical-lift aircraft to change shape during flight to optimize performance.
A study in fluid-structure interaction published by researchers with the Army Research Laboratory and Texas A&M University led to development of technology that can support rapid changes to the structural configuration of wings on Future Vertical Lift vehicles to account for how they interact with the air around them.
One of the Army’s top six modernization priorities, the Future Vertical Lift program aims to revamp current rotorcraft with technologies that improve “maneuverability, range, speed, payload, survivability, reliability, and reduced logistical footprint.” the Army said.
For some reconnaissance missions, a vehicle may need to "get quickly to station, or dash, and then attempt to stay on station for as long as possible, or loiter," ARL Aerospace Engineer Francis Phillips said. "During dash segments, short wings are desirable in order to go fast and be more maneuverable, but for loiter segments, long wings are desirable in order to enable low power, high endurance flight."
The tool will allow the wings to bend and morph, but “if the wing bends too much, then the theoretical benefits of the morphing could be negated and also could lead to control issues and instabilities," Phillips said.
Because it takes so much computation to analyze exactly how a moving wing interacts with the surrounding air -- in the range of about 10,000 core-hours for a single configuration -- the researchers developed a process that decouples the calculations for the fluid and the structure (or the air and the wings). This reduces the computational cost for a single run by as much as 80%, Phillips said.
The decoupled approach also allows for the analysis of additional structural configurations without re-analyzing the fluid, which saves even more compute time and delivers multiple orders of magnitude in computational cost reductions, ARL officials said.
Ultimately, this technology could help the Army design multi-functional Future Vertical Lift vehicles much more quickly, Phillips said. Additionally, when implemented within an optimization framework and coupled with additive manufacturing, future warfighters will be able to use this tool to manufacture optimized custom air vehicles for mission specific uses, he said.