Are modular homes the future of affordable housing?
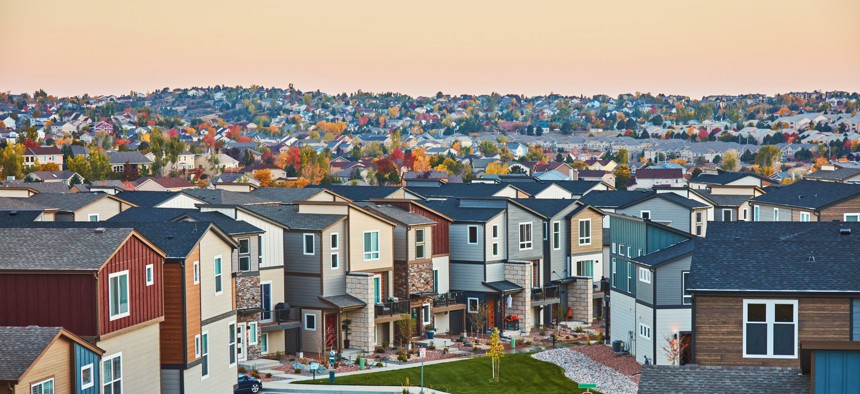
CatLane/GettyImages
In Buena Vista, Colorado, a public-private partnership crafted a patchwork of legislation, partnerships and regulatory tools to help a local company quickly deliver factory-built, affordable rental units.
This story was first posted on Reasons to Be Cheerful. Read the original here.
In Buena Vista, Colorado, there’s a factory that builds houses. Not double-wides or A-frame kits, but bonafide, full-size, single-family homes. The factory, home of the manufacturing company Fading West, is immense. Like a giant air hockey table, its floor is covered with air jets powerful enough to move whole rooms. And right now, the facility is churning out up to two homes per week.
Housing experts have toyed with the idea of modular housing as a solution to the affordable housing crisis for decades. In the 1970s, the federal government dumped millions of dollars in subsidies into modular home factories across the US. But the subsidies couldn’t change the fact that the technology wasn’t good enough to make or move the homes efficiently. Then there was the problem of the connotation. Prefabricated homes were often associated with mobile home parks, which many middle-class Americans considered shoddily made and visually unattractive. For decades, “prefab” was a bit of a dirty word.
But today, manufacturing technology has come a long way, and brands like Fading West have revolutionized both the method and look of factory-built homes.
Fading West’s, for example, are indistinguishable from traditional, stick-built housing — except for the fact that its factory can build a two-bedroom unit in nine days flat.
With that kind of speed and efficiency, some experts are touting modular homes as the future of affordable housing. If Fading West has its way, that future will start in Buena Vista.
When City Planning Director Joel Benson first moved to Buena Vista 20 years ago, he had no problem finding a place to live. He had come to this small hamlet in southern Colorado at the foot of the Rocky Mountains for its stunning views and unparalleled outdoor recreation access. He’d also found work as a ranch hand. Back then, employee housing came with the gig.
“Later, we bought a house in the area,” Benson says. “It wasn’t hard, and it wasn’t expensive.” Those glory days didn’t last long. Over the next decade, Buena Vista started to gain fame as a vacation hotspot, and more people moved to town. But mountains hem the valley on two sides. That means space is limited, and building in places this remote is notoriously expensive. The housing supply couldn’t keep up with the demand — especially when the Great Recession of 2008 put the kibosh on new development. By 2015, Buena Vista’s housing had just a one-percent vacancy rate, Benson says.
Then the pandemic hit, and things got worse.
When Covid-19 spread across the US in 2020, so did mountain-town fever. Remote workers and retirees flocked to Colorado in search of clean air, open space and an idyllic location from which to telework. At the time, mortgage interest rates were at all-time lows, and these newcomers snapped up much of the available housing stock.
Over the last decade, rents in Buena Vista have increased by an average of 43 percent, in part because of the pandemic-sparked demand. Between 2020 and 2022 alone, the average home price went up by 41 percent. That’s put homeownership out of reach for most residents and has forced lower-income families out.
“I’ve seen people lose neighbors and kids lose their friends because they can’t afford to live here,” says Read McCulloch, executive director of the Chaffee Housing Trust, a nonprofit that works on housing issues in the county where Buena Vista is located.
Housing experts hear anecdotes like these in mountain towns across America, but especially in vacation hot spots like Jackson, Wyoming, or Bozeman, Montana. While the affordable housing crisis is a nationwide issue, it hits especially hard in cities where national park borders, mountain ranges or coastlines severely restrict the amount of housing stock developers can inexpensively add. Many cities have found themselves at a breaking point: add more units fast, or watch the exodus begin.
Post-pandemic, the home-building market bounced back in many mountain towns, but the focus wasn’t on affordable housing.
“If you’re a builder, you’re going to build multimillion-dollar single-family homes because that’s what makes money,” says Ashley Kappel, executive director of the Chaffee County Housing Authority. That’s left towns like Buena Vista with a serious shortage of rental units. Fortunately, some local entrepreneurs have stepped up to help.
About six years ago, Charlie Chupp, a Buena Vista resident and now the founder and CEO of Fading West, purchased 22 acres of land in town. His plan was to develop the land — and do something about the housing crisis once and for all.
Chupp knew that to succeed, he’d have to start at the root of the issue: Buena Vista’s short building season, high cost of materials and shortage of labor.
His plan was to build a factory inspired by Toyota and other car-manufacturing giants.
With this approach, he’d be able to make homes better, faster — and more affordable — than ever before.
It seemed ambitious, but the town was on board. “Fading West recognized, ‘Hey, there’s this need, so let’s get creative with how to address it,’” says Benson, Buena Vista’s planning director. “I think that sort of ingenuity can really help address the housing issues here.”
They’re well on their way. Fading West is now in the middle of a 225-unit development on that parcel Chupp bought six years ago. The first 70 or 80 homes were built using pre-made units from a factory in Nebraska. Now, they’re made in Fading West’s $30 million, Buena Vista-based factory.
According to Eric Schaefer, Fading West’s head of business development, having a factory allows the company to streamline production, ensure tight quality control and purchase materials at significant bulk discounts. The staff are able to perfect their techniques for a limited style of homes (Fading West offers just six). And it’s easy to train new staff — many of whom are Buena Vista locals — on site.
The factory is fast. Every six hours, a home moves from one station to the next on a bed of forced air. Building a home from start to finish takes just nine days. Those numbers often raise eyebrows; Schaefer says a big part of his job is explaining that Fading West’s homes might be quick to build, but they’re also robust. “They’re built to the same standards as homes built the traditional way,” he says.
“Modular housing used to be your single- and double-wides. Today, that industry has matured significantly,” says McCulloch.
Fading West now has 170 homes in its Buena Vista development — a neighborhood dubbed The Farm. All are well-insulated, stormproof, and capable of withstanding the strong winds and heavy snows the Rockies are known for. Better yet: Most came in at prices affordable to median income-earners.
“Our goal is to make it possible for more people to become homeowners,” Schaefer says. “It’s a life-changing event when you buy your first home. It changes not just your future but that of your kids and your grandkids.”
Fading West claims it can shave 20 percent of the cost of a home with its manufacturing methods. That’s significant, but on its own, it’s not quite enough to make these homes affordable. The company still needs to rely on land-trust land — which is essentially donated to developers — and government grants and subsidies. Those kinds of public-private partnerships are currently the only way to bring housing costs down to a level considered affordable for low-income families, McCulloch says.
On its own, “Fading West is not a cure-all,” McCulloch adds. But in a place like Buena Vista where winters are so harsh that homebuilders can only work outdoors a few months out of the year, having a factory can help the town make significant headway in increasing its housing stock. And the more the housing supply grows, the more costs should begin to drop.
“This is definitely a solution. Stick-building [i.e., traditional construction] is not the answer,” says Kappel. “Modular construction has to be part of the equation. Affordable housing is a super complicated problem to solve, but building these more quickly will definitely help.”
The trend is picking up in other places, too. The city of Boulder, Colorado, is in the middle of building a 31,375-square-foot modular housing factory that will produce manufactured homes for local residents starting in late 2024. Aurora, Colorado, also passed a resolution earlier this year to increase its use of modular housing.
In Michigan, local nonprofit Seeds of Promise and modular housing enterprise InnovaLab Development have teamed up on a 25-unit community in Rapids City and a 20-unit community in Muskegon. Both are designed to serve low-income communities.
Creating an effective affordable housing strategy is often a patchwork of legislation, partnerships and regulatory tools. Fortunately, Buena Vista has a few other tricks up its sleeve. A few years ago, for example, the town realized that one of the best ways to incentivize affordable home building was to keep a tight fist on the city’s water rights. Developers who agree to build affordable housing get priority when it comes to directing the city’s scarce water supply to their developments. That makes it more likely that they’ll get the water allotments they need to launch a new project.
Many cities — including Buena Vista — have also curbed the proliferation of short-term rentals (STRs), another drain on the housing supply, by instituting license caps. If you want to turn your home into an AirBnB or VRBO, you must first secure one of just a few available STR licenses. That puts more of the city’s limited housing supply in the hands of community members.
Add to that community land trusts, government subsidies and novel building solutions like Fading West’s, and you’ve got a toolkit that’s equipped to ensure the future of mountain town neighborhoods — and the people who call them home.
Corey Buhay is a Colorado-based freelance writer and a former editor of Backpacker Magazine. You can read her work in Smithsonian, Outside, The Denver Post, Climbing and Alpinist.