Robot Chicken Butchers and Other Job Automation Brought to You By Covid
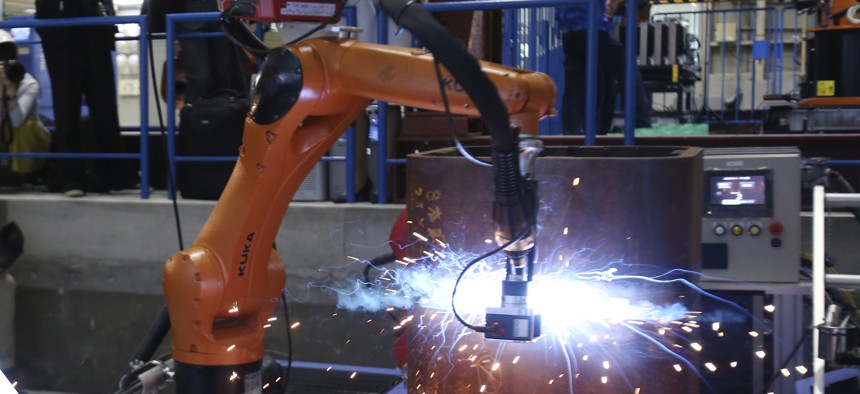
Shimizu Corp.'s Robo-Welder is demonstrated during a press tour to the major Japanese construction company's robot laboratory in Tokyo on April 23, 2018. AP Photo
Connecting state and local government leaders
The coronavirus could accelerate adoption of automation technologies as businesses look to minimize human contact.
This story was originally published by Stateline, an initiative of the Pew Charitable Trusts.
The trend toward robots and computers taking jobs people have held is getting a big push from Covid-19.
A human face behind the counter is traditionally a welcome sight, but now people are warier of close contact with strangers. That opens the door to robots taking orders, flipping burgers, even delivering room service meals.
“This was an issue for germaphobes, and now everybody is going to be a germaphobe. The future started in March,” said Johannes Moenius, a University of Redlands business professor.
Adding some robots can help factories keep up production when they must limit the number of human workers for safety’s sake. Robots can even do now-dangerous hospital jobs such as cleaning rooms and allowing doctors and nurses to communicate remotely with patients to minimize staff exposure.
In a June survey, 44% of corporate financial officers said they were considering more automation in response to coronavirus issues.
Experts and advocates say states and cities must help workers displaced by automation, though most agencies are overwhelmed with a backlog of unemployment claims they must clear first.
Employers adopting automation usually stress that workers may find it more fulfilling to do more involved tasks while robots do the grueling jobs.
Fast food chain White Castle plans to start using a robot fryer named Flippy this fall in Chicago, a measure to minimize human contact with food. The company said workers should be able to help more customers while Flippy does its “time-consuming and dangerous” job over a vat of hot oil.
A skilled welder is “a happier employee” doing complex welds while a robot does the routine stuff, according to a welding company that started using robots in Bloomer, Wisconsin, in March.
Robot welders have been popular because of pandemic worker safety issues, and because more companies are bringing back work to the United States from overseas to avoid pandemic supply chain issues. Companies also find welding robots easier to train with new phone apps, said Rob Goldiez, CEO of Nashville, Tennessee-based Hirebotics, which rents them by the month.
Meat processing plants are critical to the food supply and have stayed open, but virus outbreaks have been common in the noisy, crowded plants that often depend on shouted communication, which can spread the virus.
Tyson Foods, which already was experimenting with automation, sped up work on a robot chicken butcher in recent months, citing increased urgency because of the pandemic.
Jobs also could be automated for better-educated knowledge workers, including some computer programmers, medical assistants and sales professionals. For example, some convention planners and IT workers depend on conventions, large meetings and office computer systems endangered by new work-at-home policies and travel bans.
“The new generation is now more adept and amenable to meetings being held online and distance learning. They now realize you don’t have to travel to a convention in Las Vegas or Orlando or New Orleans,” said John Restrepo, a Las Vegas-based economic consultant. “This is going to have a permanent effect.”
Before the pandemic, Moenis, the University of Redlands professor, predicted the largest share of jobs at risk were in Sun Belt migration magnets, such as Orlando, Florida, inland California and Las Vegas. COVID-19 threatens more of those jobs, even the customer service jobs once deemed safe.
Those areas have drawn flocks of new residents looking for warm weather, recreation and a low cost of living. But the resulting jobs are low-wage gigs in stores and restaurants that cater to tourists and retirees, the kind of jobs now threatened by robot workers.
Parts of North and South Carolina, Texas, Kentucky and Indiana also are particularly vulnerable, according to Moenius’ 2017 study, because of low-skill jobs in mining or factories that can be performed by machines.
States and cities have a responsibility to help workers displaced by automation, since employees who lose their job to automation often turn to lower-paying service jobs, Brookings Institution experts argued in a report last year. Such workers need financial help and training to adjust to new jobs, the report concluded.
But the pandemic likely will delay such plans, said Mark Muro, an author of the report and a policy director at Brookings, because state labor agencies are buried under unemployment claims.
“After that, the first thing is to support creation of jobs. I think virtually all states understand that,” Muro said. “With this extraordinary unemployment, you have to match people to available jobs when automation is quietly chipping away at them.”
Rural areas, where companies have built many factories because of lower labor costs, are particularly vulnerable to “task replacement” by robots and other machinery, according to the Brookings report.
Moenius agreed that helping workers acquire skills will improve their job security.
“We have to have a skills offensive, in terms of pushing and appealing and squeezing and whatever we can to support workers stepping up the ladder and acquiring more skills,” Moenius said.
But some workers may not make that transition from factory work to fixing and programming robots and computers.
“Not everybody is going to learn to code,” said Patrick Dicks, who spent time last year talking to factory workers in rural South Carolina for his doctoral dissertation at Robert Morris University in Pennsylvania. He’s since heard from some workers worried about coronavirus outbreaks in factories such as one in a Bridgestone Tire plant in Aiken County.
Factory jobs are especially important in South Carolina, where 19 of 46 county economies are dependent on manufacturing, according to the Economic Research Service at the U.S. Department of Agriculture, a rate behind only Indiana and similar to Ohio and Wisconsin.
“If they lose the job they’re in, they may be completely lost,” Dicks said. “These are people who just want to work with their hands, to make something. I don’t think they know what’s coming.”
Even those predicting vast workplace changes over the next 20 years, like Moenius, were surprised at how coronavirus fears have moved automation to center stage.
An Oxford University study in 2017 found that 86% of restaurant jobs, 85% of manual labor and 92% of retail sales jobs could be automated. Moenius said he initially thought it would happen by 2035 but the pandemic has pushed that timeline up as much as five years.
Now, fast food venues everywhere are adding kiosks for contact-free ordering, department stores are dropping off automated orders at the curb, and robots are delivering towels and room service at Hilton and Marriott hotels.
“Two years ago, I was saying that customer interaction was something people value, that you would always need people in that role,” Moenius said. “The pandemic has pushed everything forward.”
NEXT STORY: Health Care Workers of Color Nearly Twice as Likely as Whites to Get Covid-19